The Comprehensive Guide to Hydraulic Balls: Revolutionizing Fluid Control
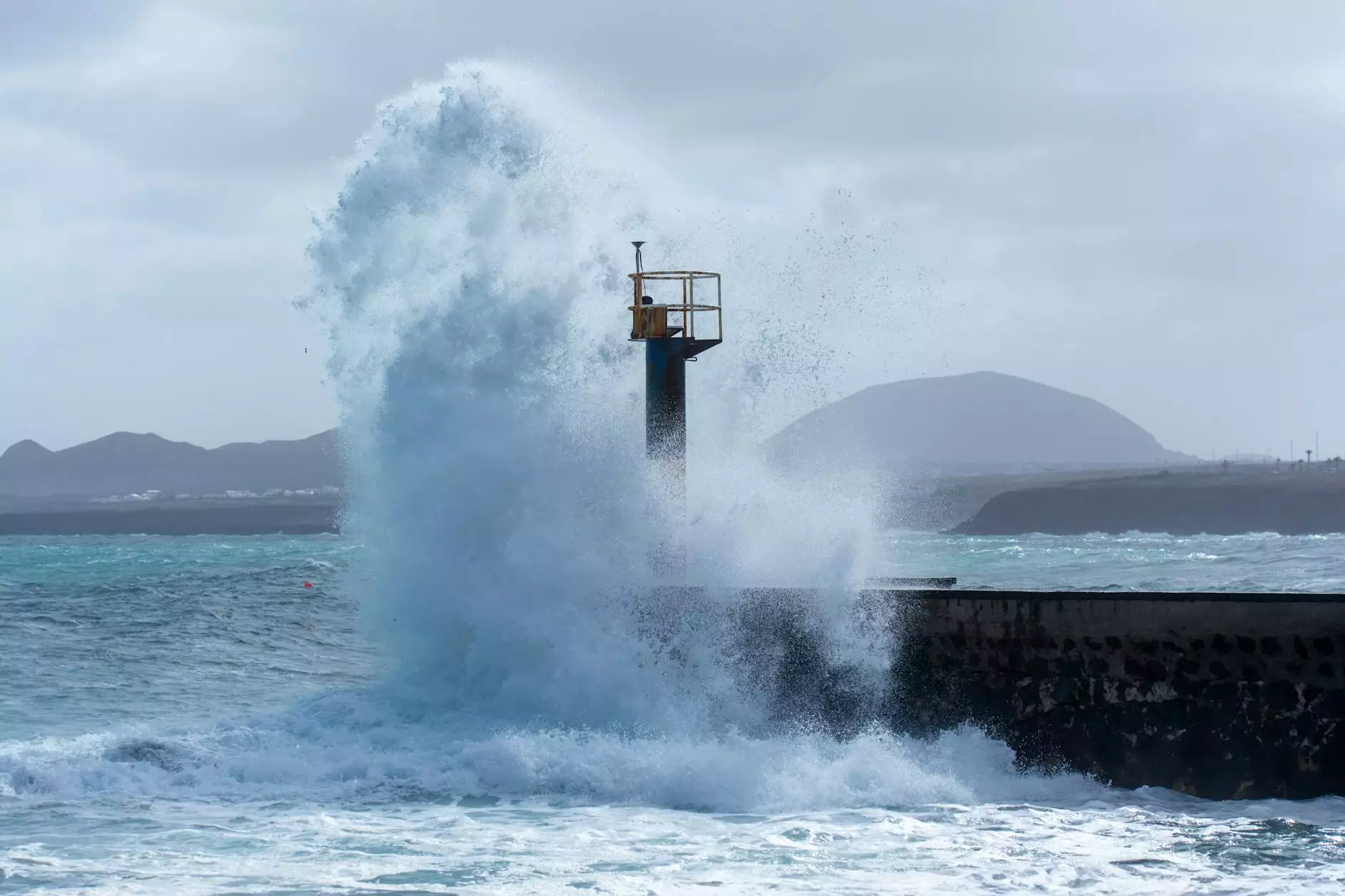
In the world of fluid dynamics, hydraulic balls have emerged as a pivotal component that contributes to the efficiency and reliability of various systems. Whether utilized in industrial, automotive, or aerospace applications, hydraulic balls play a crucial role in managing and controlling the flow of fluids. This article delves deep into the significance of hydraulic balls, their functionality, advantages, and applications across multiple sectors.
Understanding Hydraulic Balls
Hydraulic balls are spherical components typically made from durable materials like stainless steel, brass, or plastic. They are commonly used to control the flow and pressure of liquids in hydraulic systems. The basic principle behind hydraulic balls is straightforward: they can either obstruct or allow the passage of fluid, depending on their position and operation method.
These balls are often employed within a valve mechanism, which can be activated manually or through automated systems. By rotating the ball, the opening can be aligned with the inlet and outlet ports of the fluid system, effectively regulating flow.
Key Components of Hydraulic Balls
The functionality of hydraulic balls can be attributed to several key components:
- Body: The main structure of the hydraulic ball that houses the flow path.
- Seal: A critical component that prevents leakage and ensures tight closing.
- Actuator: The mechanism used to turn the hydraulic ball, which can be manual, pneumatic, or electric.
- Ports: Inlet and outlet openings that facilitate the flow of fluid.
The Functionality of Hydraulic Balls
The operation of hydraulic balls is primarily governed by their unique design and the principles of hydraulics. When the hydraulic ball is turned, it either blocks or allows fluid to flow through the valve. This functionality can be broken down into several operational modes:
- Open Position: In this position, the flow of fluid is unrestricted, allowing for maximum flow rates.
- Closed Position: The ball is turned to block the passage, effectively stopping fluid movement.
- Throttling Mode: By partially opening the valve, operators can control the flow rate of the fluid, which is vital in systems requiring precise flow management.
Types of Hydraulic Balls
Different types of hydraulic balls are available to meet the diverse needs of various industries:
- Standard Hydraulic Balls: Commonly used in a variety of applications, featuring a straightforward design.
- High-Pressure Hydraulic Balls: Designed to withstand extreme pressure conditions, suitable for oil and gas applications.
- Corrosion-Resistant Hydraulic Balls: Made from materials resistant to corrosive substances, ideal for chemical processing.
Advantages of Using Hydraulic Balls
One of the primary reasons for the widespread adoption of hydraulic balls in industrial applications is their numerous advantages:
1. Enhanced Control
The ability to control fluid flow with precision is critical in many applications. Hydraulic balls allow for accurate regulation, which can lead to improved process control and efficiency.
2. Reliability and Durability
Manufactured from robust materials, hydraulic balls demonstrate exceptional durability and resistance to wear and tear, ensuring a long operational life even under challenging conditions.
3. Ease of Maintenance
Hydraulic ball systems are designed for easy access, making maintenance and inspection straightforward. Regular servicing can significantly extend the lifespan of the components.
4. Versatility
Whether in a manufacturing facility, a vehicle, or an industrial plant, hydraulic balls can be customized for a wide range of applications, making them adaptable across various fields.
Applications of Hydraulic Balls
The versatility of hydraulic balls means they find applications in numerous industries:
1. Manufacturing
In manufacturing processes, hydraulic balls are employed to control the flow of oils, water, and other fluids essential for machinery operation, thereby improving overall productivity.
2. Automotive
Hydraulic balls are integral components in automotive systems, specifically in brake and power steering systems, where they assist in fluid management.
3. Aerospace
In the aerospace sector, the precision and reliability of hydraulic balls are crucial for controlling fluids in hydraulic systems that power aircraft landing gear and flight control surfaces.
4. Oil and Gas
In this highly regulated industry, high-pressure hydraulic balls are essential for safely managing the flow of crude oil and natural gas, helping to maintain operational efficiency and safety.
5. Chemical Processing
Corrosion-resistant hydraulic balls are commonly used in chemical processing plants to handle corrosive fluids safely and effectively.
Choosing the Right Hydraulic Ball
When selecting the appropriate hydraulic ball for your application, consider the following factors:
- Material: Choose materials based on the type of fluids being handled and the operating environment.
- Pressure Rating: Ensure the hydraulic ball can withstand the maximum pressure exerted in your system.
- Size: Assess the dimensions to ensure compatibility with existing systems.
- Type of Actuation: Determine whether a manual or automated actuation system best suits your operational needs.
Conclusion
In conclusion, hydraulic balls serve as a fundamental component in various fluid control systems across multiple industries. Their ability to provide precise flow and pressure control, combined with their reliability and versatility, makes them indispensable in today's advanced manufacturing and automotive landscapes. By understanding the functionality, advantages, and diverse applications of hydraulic balls, businesses can make informed decisions that enhance operational efficiency and safety.
At FITSCH, we offer a comprehensive range of fittings and hydraulic ball solutions that cater to various industrial needs. Our products are engineered for quality and performance, ensuring that you can confidently rely on them in your critical operations.