The Comprehensive Guide to Plastic Mold Manufacturing
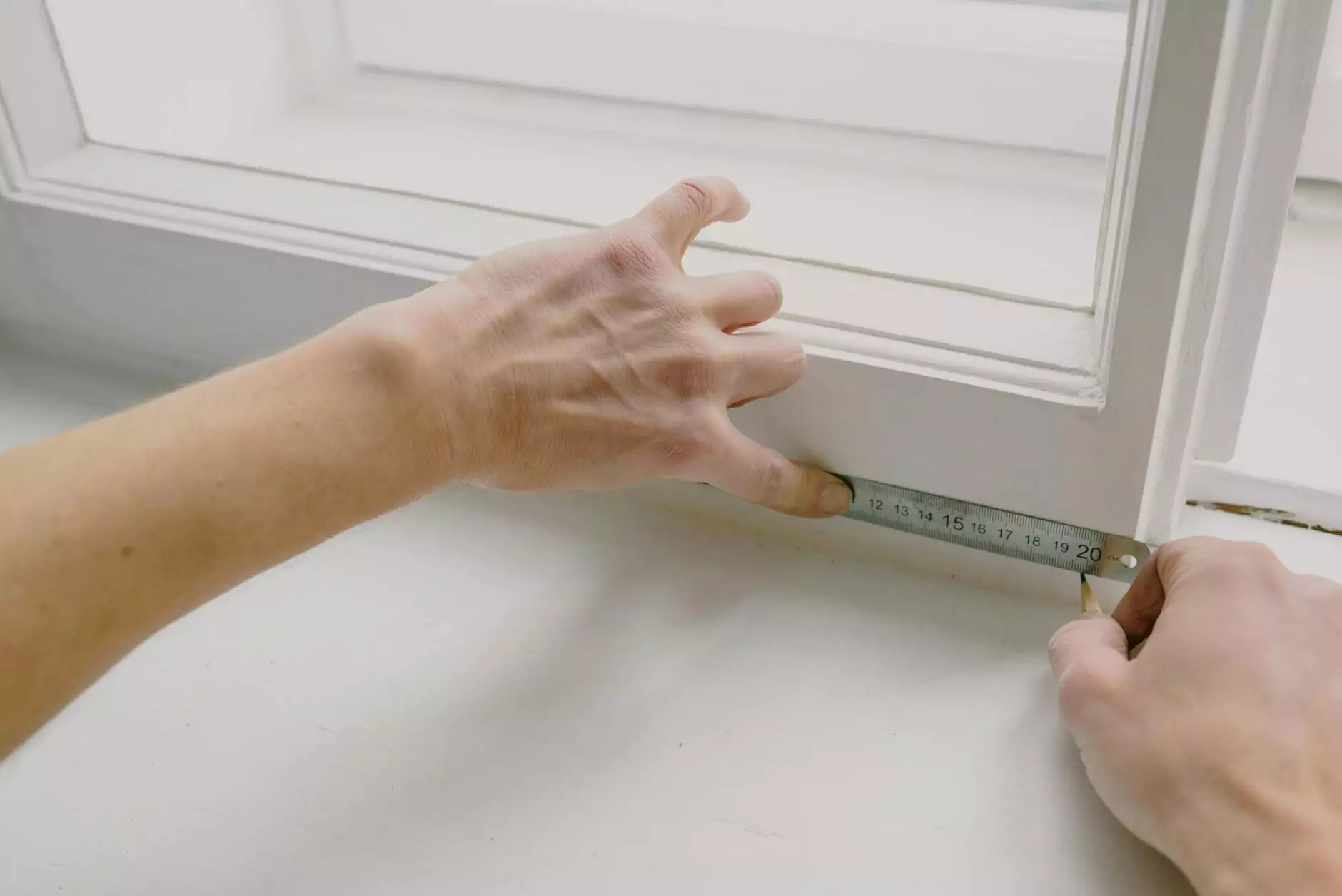
Plastic mold manufacturing plays a pivotal role in various industries by enabling the mass production of plastic components with unmatched precision and efficiency. As a foundational pillar of the manufacturing sector, understanding the intricacies of this process is essential for businesses aiming to leverage modern technologies in their production lines. In this guide, we will delve deeply into the various facets of plastic mold manufacturing, touching upon its processes, benefits, applications, and how companies like DeepMould are leading the charge in innovative metal fabrication.
What is Plastic Mold Manufacturing?
At its core, plastic mold manufacturing is the process of creating parts by injecting molten plastic into a mold. This method allows for the rapid production of high-quality components, making it favored by manufacturers around the globe. The two predominant types of molds used in this process are:
- Injection Molds: Used for injecting plastic material into the mold cavity.
- Blow Molds: These molds are employed to form hollow plastic parts.
The versatility of these molds means they can produce anything from intricate designs to simple shapes, catering to a wide array of industries such as automotive, consumer goods, and medical devices.
The Plastic Mold Manufacturing Process
The plastic mold manufacturing process involves several well-defined steps. The following is a detailed overview of each stage:
1. Design and Prototyping
The initial stage in plastic mold manufacturing is the design of the mold. Using CAD (Computer-Aided Design) software, manufacturers create detailed 3D models of the components to be produced. Prototyping is essential as it allows for testing designs and ensuring feasibility, reducing errors that may arise during production.
2. Mold Fabrication
After the design phase, the mold is fabricated. This involves high-precision machining techniques to create the mold cavity. Materials such as steel or aluminum are commonly used due to their durability and ability to withstand the injection process. Technologies such as CNC (Computer Numerical Control) machining and EDM (Electrical Discharge Machining) are leveraged here to achieve precision.
3. Injection Molding Process
The actual plastic mold manufacturing occurs during the injection molding phase. The process can be broken down into several steps:
- Heating: The plastic pellets are heated until they become molten.
- Injection: The molten plastic is injected into the mold cavity at high pressure.
- Cooling: Once injected, the plastic cools and solidifies into the desired shape.
- Demolding: The mold opens, and the finished part is ejected.
Benefits of Plastic Mold Manufacturing
Companies across various sectors favor plastic mold manufacturing for numerous reasons. The key benefits include:
- Cost-Effectiveness: Once the initial mold is created, manufacturing each unit is relatively inexpensive, making it ideal for large production runs.
- Consistency: The injection molding process offers high precision, ensuring that each part produced is identical to the last.
- Flexibility: With advancements in technology, molds can be designed to accommodate various materials and complex geometries.
- Reduced Waste: The efficiency of the injection process minimizes material wastage, making it an environmentally friendly option.
- High Production Speed: The cycle times in injection molding can often be measured in seconds, greatly speeding up the time to market.
Applications of Plastic Mold Manufacturing
The scope of applications for plastic mold manufacturing is vast. Some notable areas include:
1. Automotive Industry
From dashboards to custom plastic components, the automotive industry relies heavily on plastic mold manufacturing for lightweight, durable parts.
2. Consumer Goods
Everyday products such as packaging, toys, and appliances benefit from the efficiency and cost-effectiveness of this manufacturing method.
3. Medical Devices
The medical field requires high precision and reliability, which is why plastic mold manufacturing is extensively used for devices and components like syringes and surgical instruments.
4. Electronics
Plastic molds are crucial for creating housings, connectors, and other components used in consumer electronics, providing insulation and protection for sensitive parts.
Technological Innovations in Plastic Mold Manufacturing
Advancements in technology continue to enhance the field of plastic mold manufacturing. Innovations such as:
- 3D Printing: Employed for rapid prototyping, allowing for faster iterations and adjustments.
- Smart Molds: Incorporation of sensors to monitor the injection process in real time for improving quality control.
- Advanced Materials: The introduction of new types of plastics that offer superior strength, flexibility, and heat resistance.
DeepMould: Your Partner in Metal Fabrication
At DeepMould, we specialize in delivering top-notch solutions for plastic mold manufacturing and metal fabricators. Our expertise is backed by years of experience, state-of-the-art technology, and a commitment to quality. We believe in fostering innovation while ensuring that our customers receive tailored solutions that meet their specific needs.
Commitment to Quality
Quality is at the forefront of our manufacturing processes. We implement rigorous quality control measures at every stage of production to ensure that our customers receive components that adhere to the highest standards.
Tailored Solutions
At DeepMould, we understand that every project is unique. Our team works closely with clients to offer customized solutions that align with their goals and specifications.
Conclusion: Embracing the Future of Plastic Mold Manufacturing
The landscape of plastic mold manufacturing is continually evolving, presenting exciting opportunities for businesses willing to embrace innovation. With its myriad benefits and applications, this manufacturing process is indispensable in today's industrial world. Partnering with experts like DeepMould ensures that you are well-equipped to navigate this dynamic environment, drive efficiency, and achieve outstanding results.
Call to Action
If you are looking to enhance your production capabilities with high-quality plastic molds, contact DeepMould today! Our team is ready to assist you in realizing your manufacturing goals and revolutionizing your production processes.