Prototype Molding Services Suppliers: The Key to Successful Business Ventures
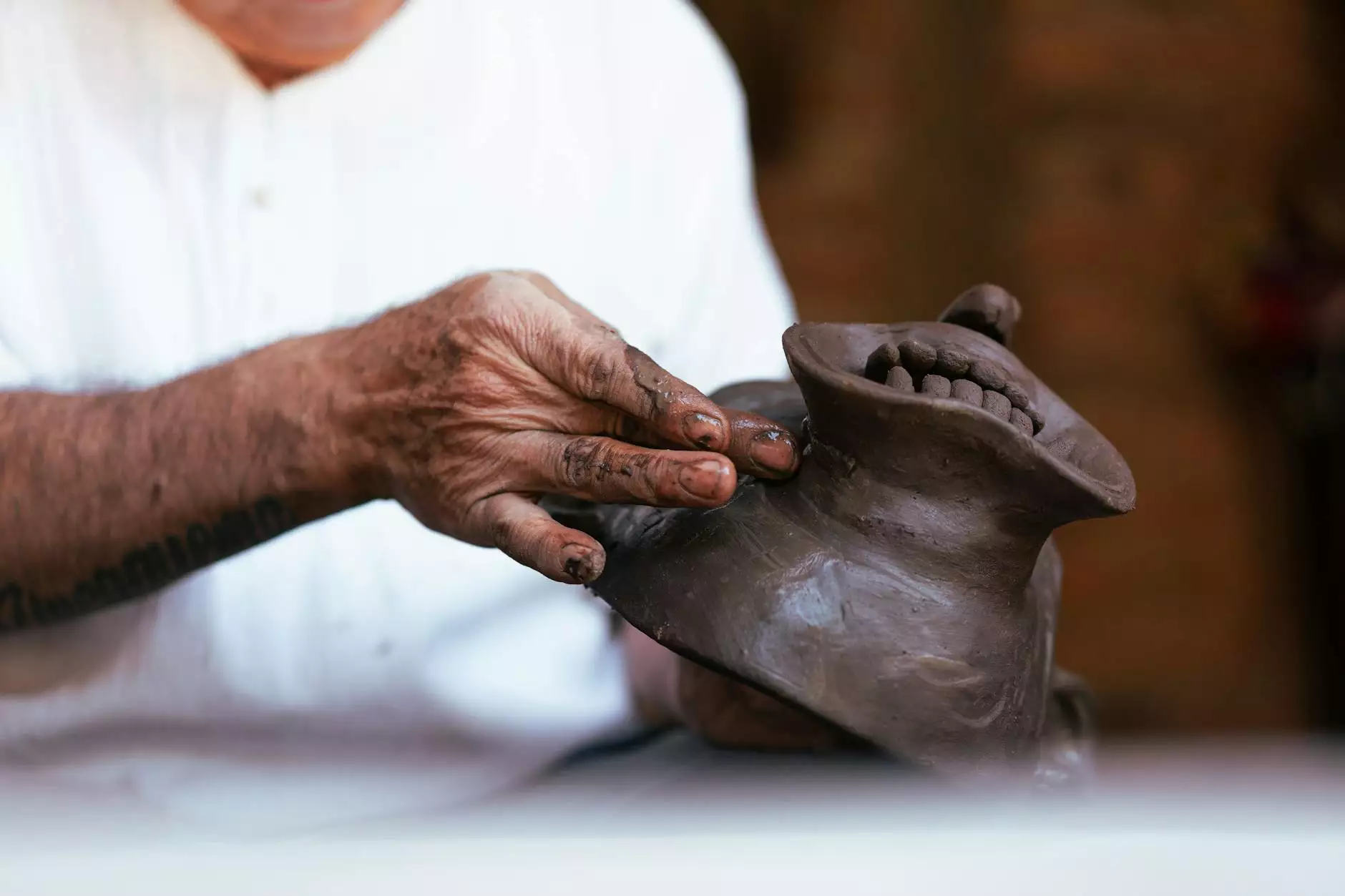
The world of manufacturing is constantly evolving, and prototype molding services suppliers play a pivotal role in this transformation. As businesses seek to innovate and improve their products, the need for high-quality prototype molding services grows exponentially. In this comprehensive guide, we will explore what prototype molding is, the critical factors to consider when choosing a supplier, and how the right partnership can elevate your business.
Understanding Prototype Molding
Prototype molding involves creating a preliminary version of a product to test its design, functionality, and manufacturability before full-scale production. This process is crucial for companies aiming to reduce risks, save costs, and streamline their production process. Prototype molding allows manufacturers to refine their products based on real-world testing and feedback, ensuring the final product meets market demands.
The Importance of Prototype Molding
- Cost Efficiency: By identifying design flaws early, businesses can avoid costly changes during mass production.
- Time Savings: Quick iterations allow for faster product development cycles.
- Market Validation: Prototypes enable businesses to gather customer feedback before making significant investments.
- Risk Reduction: Testing prototypes helps mitigate the risks associated with product failures.
Key Factors to Consider When Choosing Prototype Molding Services Suppliers
Finding the right prototype molding services suppliers can significantly impact the success of your product development process. Here are some essential factors to consider:
1. Experience and Expertise
It's crucial to select suppliers with extensive experience in prototype molding services. Look for companies that have a proven track record in your specific industry. Experienced suppliers will have the necessary skills to address your unique challenges and provide valuable insights throughout the development process.
2. Technology and Equipment
Innovative technology and state-of-the-art equipment are essential for high-quality prototype molding. Ensure that the suppliers you consider invest in the latest technology to deliver accurate and efficient prototypes. Advanced machines such as CNC milling and 3D printers can significantly enhance the molding process.
3. Material Selection
Different projects require different materials. A reliable supplier should offer a wide range of materials, including thermoplastics, metals, and composites. This versatility allows businesses to choose the best materials for their prototypes, impacting durability, weight, and cost.
4. Lead Time and Flexibility
In today's fast-paced market, timelines can be tight. It’s vital to work with suppliers who can meet your deadlines without compromising on quality. Additionally, flexibility in accommodating changes to your design during the development process is a significant asset that should not be overlooked.
5. Quality Assurance
The supplier's commitment to quality assurance measures is vital in ensuring that your prototypes meet exact specifications. Inquire about their quality control processes, certifications, and any industry standards they adhere to.
The Prototype Molding Process Explained
Understanding the prototype molding process can help you communicate effectively with your chosen supplier and set clear expectations. Here’s an overview of the typical steps involved:
Step 1: Concept Development
The process begins with a detailed concept of the product. This includes sketches, designs, and specifications that outline the product's functionality and aesthetics. Collaboration between your design team and the supplier’s engineers can lead to a more refined concept.
Step 2: Material Selection
Once the design is solidified, the next step is selecting the appropriate materials. Factors such as the prototype's intended use, mechanical properties, and cost will influence this decision. A knowledgeable supplier can provide guidance on the best material options available.
Step 3: Prototyping Techniques
Select a suitable prototyping technique based on your specifications. Common methods include:
- Injection Molding: Best for high-volume production and complex designs.
- 3D Printing: Ideal for rapid prototyping and intricate designs.
- CNC Machining: Excellent for precision parts with tight tolerances.
Step 4: Testing and Refinement
After the prototype is created, thorough testing is conducted to assess its functionality, durability, and overall design. This feedback is crucial for making necessary adjustments before proceeding to mass production.
Step 5: Finalization and Production
Once testing is complete and adjustments are made, the prototype is finalized, and you can move forward with confidence to full-scale production, knowing that the design has been validated.
Why Partner with Deep Mould for Your Prototype Molding Needs?
At Deep Mould, we pride ourselves on being one of the leading prototype molding services suppliers in the industry. Here are a few reasons why partnering with us can transform your product development journey:
1. Expertise in Metal Fabrication
With extensive experience in metal fabrication, we understand the nuances of working with various metals and their properties. This knowledge allows us to provide insights that can enhance your product’s design and functionality.
2. State-of-the-Art Facilities
Our advanced facilities are equipped with cutting-edge technology and machinery, enabling us to produce high-quality prototypes quickly and efficiently. We continuously invest in new technologies to stay ahead of industry trends.
3. Customized Solutions
We recognize that each project is unique. Our team works closely with clients to understand their specific needs and provide customized solutions that align with their vision and objectives.
4. Commitment to Quality
Quality is at the forefront of everything we do. We adhere to strict quality assurance protocols to ensure that every prototype we produce meets the highest standards. Our certifications and satisfied clients testify to our dedication to quality.
5. Supportive Team
Our knowledgeable team is here to support you every step of the way. From concept development to final production, we provide guidance and expertise to help you achieve your goals seamlessly.
Conclusion: Your Next Steps
As you embark on your product development journey, partnering with the right prototype molding services suppliers is critical to success. Take the time to research potential partners, focusing on their experience, technology, and commitment to quality.
With Deep Mould, you are not just choosing a supplier; you are selecting a partner who is dedicated to your success. Our expertise in metal fabrication and prototype molding will help you navigate the complexities of product development and bring your ideas to life.
Ready to take the next step? Reach out to us today to discuss your prototype molding needs and discover how we can help you succeed in the competitive marketplace.