Pump Cavitation: Understanding the Phenomenon and Its Impact on Business Operations
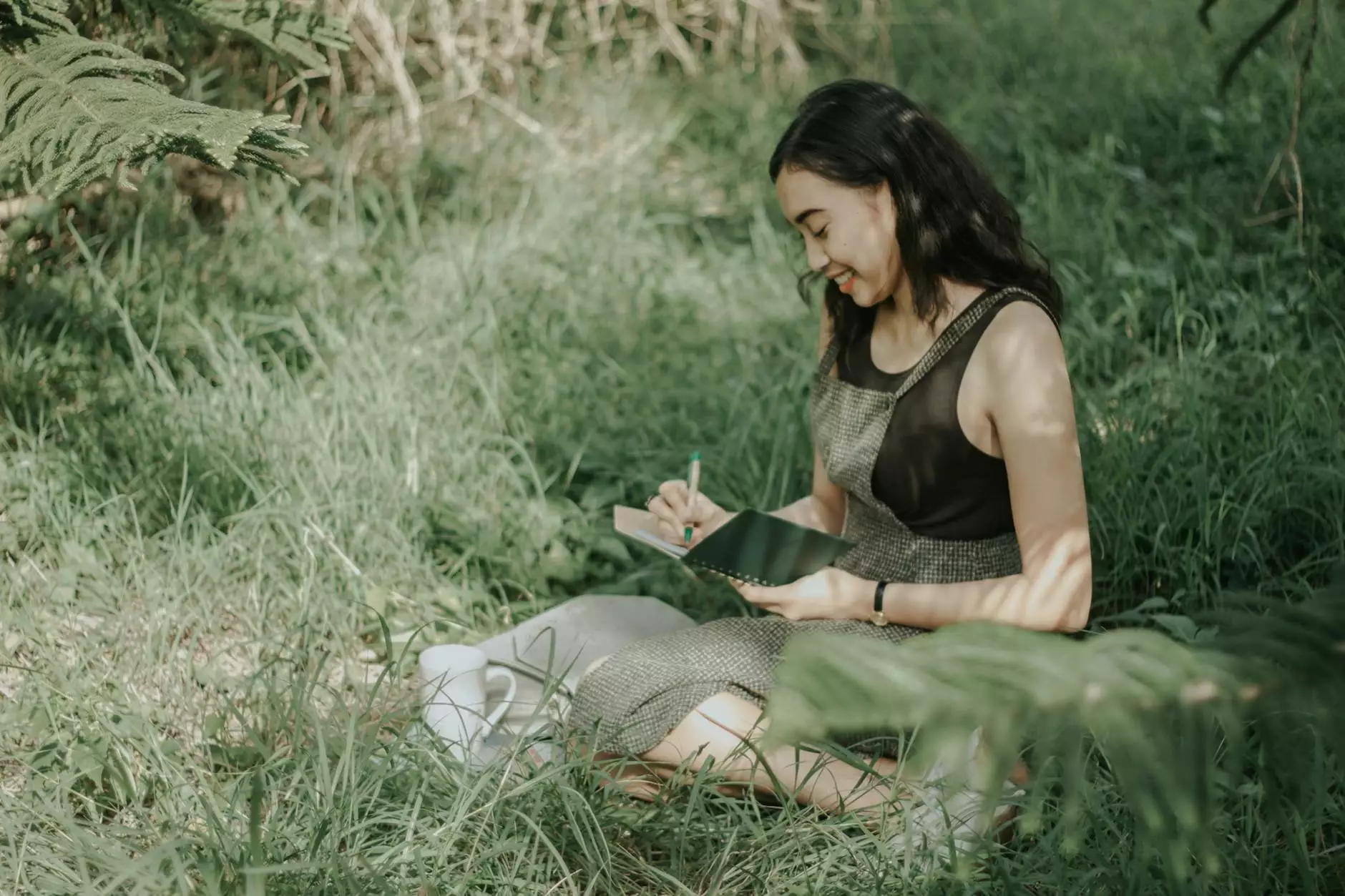
Pump cavitation is a critical phenomenon that affects various industries, particularly those involved in fluid mechanics such as auto repair, farm equipment repair, and structural engineering. Understanding this occurrence is essential for maintaining efficient and effective operations in these fields. In this comprehensive article, we will delve into the intricacies of pump cavitation, how it affects business operations, and the strategies to mitigate its impacts.
What is Pump Cavitation?
At its core, pump cavitation refers to the formation and collapse of vapor bubbles within a liquid being transported by a pump. This phenomenon occurs when the pressure of the liquid falls below its vapor pressure, leading to the creation of small vapor-filled cavities. When these bubbles travel to regions of higher pressure within the pump, they collapse violently, producing shock waves that can cause significant damage to the pump components.
The Causes of Pump Cavitation
Understanding the causes of pump cavitation is crucial for businesses that rely on hydraulic systems. The main contributors include:
- Low Pressure: If the pressure at the pump inlet is too low, it can lead to cavitation. This situation often occurs due to restrictions in piping or insufficient liquid supply.
- High Fluid Temperatures: Increased temperatures can reduce the liquid's density and elevate vapor pressure, making cavitation more likely.
- Excessive Pump Speed: Operating the pump beyond its designed speed can create conditions for cavitation, as it increases the velocity and decreases pressure.
- Improper Pump Selection: Choosing a pump with incorrect specifications for the intended application can lead to cavitation issues.
Effects of Pump Cavitation on Business Operations
The consequences of pump cavitation can have a profound impact on businesses:
1. Damage to Equipment
One of the most immediate effects of pump cavitation is physical damage to the pump itself. The collapsing vapor bubbles create shock waves that can erode metal surfaces, leading to:
- Pitting: Small depressions in the pump material.
- Metal Fatigue: Reduction in the overall strength of the pump materials.
- Seal and Bearing Failure: Increased wear on seals and bearings which can lead to leaks and further operational issues.
2. Reduced Efficiency
Pumps operating under cavitating conditions can experience a decline in efficiency, undermining productivity. The energy loss associated with cavitation can increase operational costs, leading to:
- Higher Energy Consumption: Systems may require more power to deliver the same flow rate.
- Increased Operational Costs: With less efficiency comes higher costs in terms of maintenance and energy.
3. Operational Downtime
When cavitation leads to equipment failure, businesses face operational downtime. This downtime can be detrimental, especially in sectors like auto repair and agriculture, where timely service is critical. The costs associated with downtime include:
- Lost Revenue: Each minute a pump isn’t operational can lead to significant revenue losses.
- Repair Costs: Repairing or replacing damaged equipment incurs direct costs.
- Delayed Services: In industries like auto repair, delays can result in lost customers and diminished reputation.
Identifying Cavitation: Signs and Symptoms
Recognizing the signs of cavitation early can help mitigate its effects. Common indicators include:
- Unusual Noises: A characteristic 'gravel' or 'marbles' sound often indicates cavitation.
- Vibration: Increased vibration levels can signal cavitation and should be monitored closely.
- Pump Inefficiency: A noticeable decrease in pump performance or flow rates can be a telltale sign.
Preventing Pump Cavitation
Preventing pump cavitation is vital for maintaining operational integrity. Here are essential strategies to keep in mind:
1. Proper System Design
Designing a hydraulic system with cavitation prevention in mind is crucial. This includes:
- Correct Pipe Sizing: Ensure pipes are adequately sized to maintain the necessary pressure at the pump inlet.
- Minimizing Restrictions: Reduce bends and fittings that can lower fluid pressure.
- Provision for Fluid Expansion: Ensure that your design accommodates thermal expansion of fluids.
2. Regular Maintenance
Conducting routine maintenance can help identify and resolve issues before they escalate. Key maintenance practices include:
- Regular Inspections: Regularly inspect pumps for wear, noise, and vibration issues.
- Fluid Quality Checks: Monitor fluid temperatures and quality to ensure optimal operating conditions.
- Prompt Repairs: Address vulnerabilities in your pumps and systems immediately to prevent cavitation.
3. Operating Conditions Monitoring
Monitoring your systems in real-time can provide insights into potential issues. Consider using:
- Pressure Sensors: Utilize sensors to continuously monitor pressure at key points.
- Flow Meters: Implement flow meters to detect inconsistencies that may signal cavitation.
- Temperature Sensors: Keep an eye on temperatures to maintain optimal fluid characteristics.
Addressing Pump Cavitation: Solutions and Remedies
If your business is already experiencing pump cavitation, several solutions can help mitigate the issue:
1. Cavitation-Resistant Pumps
Investing in cavitation-resistant pump technology can drastically reduce issues related to cavitation. These pumps are designed to withstand high pressure and adverse conditions.
2. Installation of Inlet Strainers
Installing inlet strainers can help ensure that the pump receives clean fluid, minimizing the risks posed by impurities that may lead to cavitation.
3. Flow Control Valves
Integrating flow control valves can help maintain pressure and flow rates within optimal ranges, reducing the chances of cavitation occurring.
Conclusion
In conclusion, understanding pump cavitation is essential for businesses in the auto repair, farm equipment repair, and structural engineering sectors. Recognizing the causes and effects of cavitation allows businesses to take proactive measures in preventing it, ultimately enhancing the efficiency and longevity of their equipment. By implementing the preventive strategies discussed, businesses can ensure operational integrity and avoid the costly ramifications of this often misunderstood phenomenon.
As the landscape of engineering and technology continues to evolve, keeping abreast of best practices in pump operations will safeguard the achievements of your enterprise. Remember, investing in knowledge and preparation is the foundation of success in any business environment.